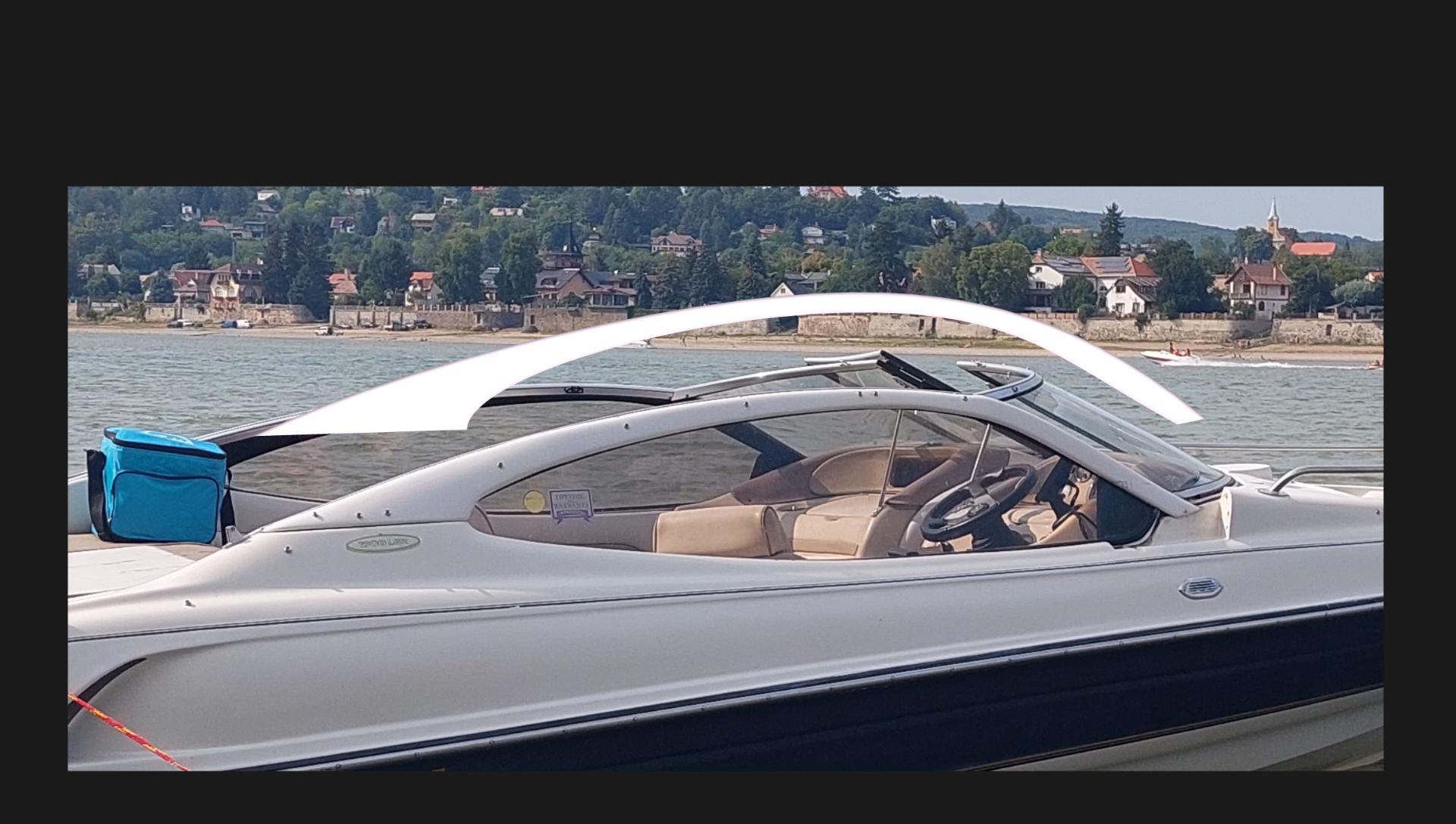
More references
Production with the additivBoat plastic componente process
Task
A part of a motorboat hull component is lost. The original parts have been made using a traditional composite laminating process, where the majority of the costs are due to template manufacturing of sufficient quality. Template quality is important because the final product surface finish depends on the template quality.
A template is a tool for producing a finished product. In this case, the production costs are high because a template capable of producing multiple parts must be manufactured even for one single part.
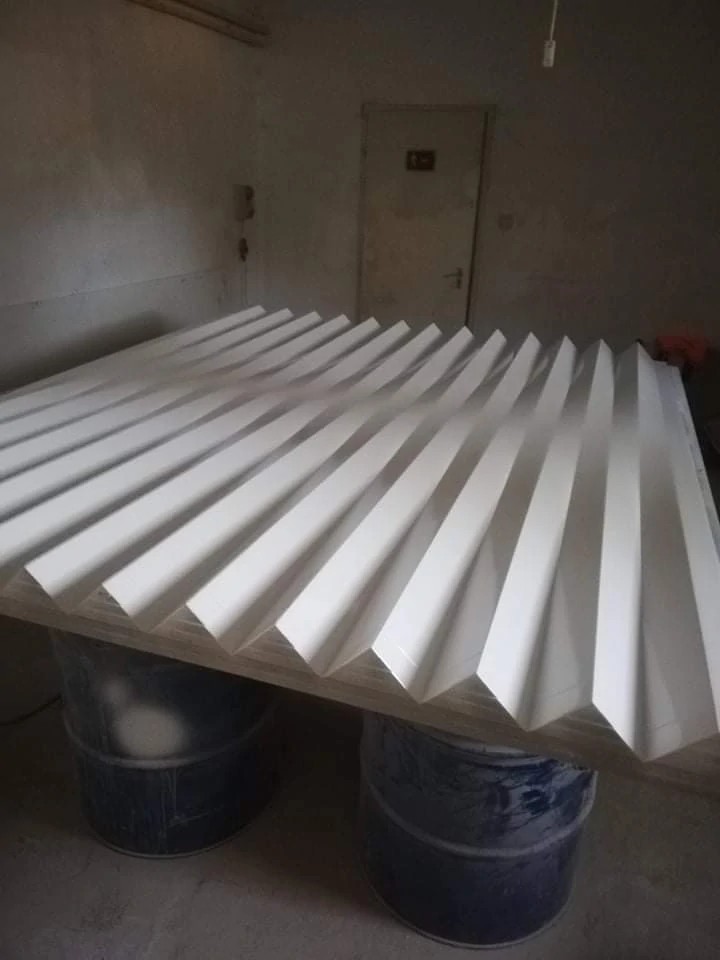
Additive manufacturing can be an excellent solution for just such cases, and in this case, the workflow is as follows:
- In this case, we were lucky because we could use the right side part as a sample, which we could 3D scan to get dimensions and geometry, as the special curves did not allow us to measure with measuring tools. We worked with Artec's Eva Lite 3D metrology scanner.
- A scanned digital file (STL) is the basis for creating a CAD model for 3D printing. The CAD model was drawn with the CAD software Rhinoceros 7, which has the major advantage of being able to check the continuity of the curves defining the shape, called Zebra analysis.
- The original part is more than 2 metres long, so an important part of the design is to ensure that the CAD model is tailored to the workspace of the chosen additive process and that the joints are mechanically and aesthetically acceptable.
- Selected process: FDM, range: x = 450 * y = 450 * z = 450 mm
- Due to the FDM process, finishing including sanding, UV painting, and glueing is required to achieve the proper surface quality of the parts.
CAD model
We are glad to work on similar projects, contact us!