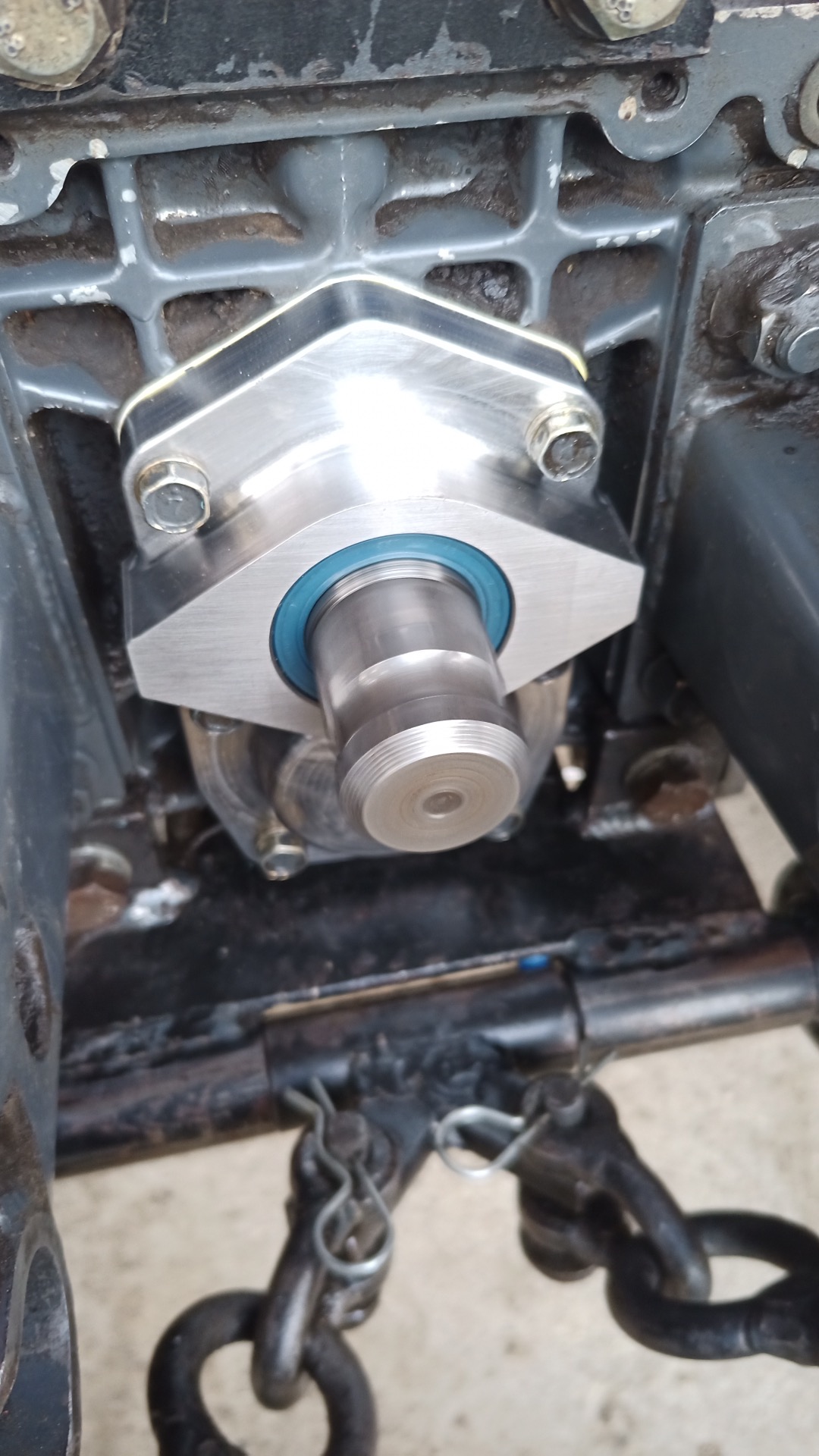
More reference
Rebuilding a cracked cast iron cover of a Kubota tractor Cardan drive
Task: CAD modelling of a cracked cardan drive cover on a 12 HP Kubota small tractor and preparation of a technical drawing for CNC remanufacturing.
Processes for creating a CAD model:
- Checking the sample provided by the client, looking for defects or damages that need to be corrected when creating the new CAD model.
- Since the geometry of the sample features no fixed measuring points, the exact dimensions can only be obtained by scanning. Preparing the sample for scanning.
- The shiny surfaces are treated with a matte, so-called scanner spray, which coats the sample with a white powder 1-2 microns thick. Once glaring is eliminated, the scanning will be successful.
- The point cloud created as a result of scanning is used to create the mesh file, which is the basis for the creation of the accurate CAD model.
- Preparation of a CAD model taking into account the specifications of the selected production process. In this case, the remanufacturing will be done using the CNC process.
- Comparison of the finished CAD model with the scanned mesh. With the Artec Studio 17 software, you can check the dimensional differences between the CAD model and the scanned mesh model, such as the accuracy of holes and geometries, on a graph with one-hundredth accuracy.
- Preparation of technical drawings to support CAD model production.
- Delivery of CAD model and documentation to the customer.
Modelling process: